Not known Details About Alcast Company
Not known Details About Alcast Company
Blog Article
The smart Trick of Alcast Company That Nobody is Discussing
Table of ContentsAlcast Company Can Be Fun For Anyone5 Simple Techniques For Alcast CompanySome Known Factual Statements About Alcast Company Everything about Alcast CompanyRumored Buzz on Alcast CompanyAlcast Company for Dummies
Chemical Contrast of Cast Light weight aluminum Alloys Silicon advertises castability by minimizing the alloy's melting temperature level and enhancing fluidness throughout spreading. Additionally, silicon contributes to the alloy's stamina and use resistance, making it valuable in applications where sturdiness is critical, such as auto components and engine components.It also enhances the machinability of the alloy, making it easier to refine into finished products. In this way, iron contributes to the total workability of aluminum alloys. Copper boosts electric conductivity, making it useful in electric applications. It additionally boosts deterioration resistance and contributes to the alloy's general toughness.
Manganese adds to the stamina of aluminum alloys and boosts workability (Foundry). It is typically made use of in wrought light weight aluminum products like sheets, extrusions, and profiles. The visibility of manganese help in the alloy's formability and resistance to breaking throughout construction processes. Magnesium is a light-weight component that gives strength and impact resistance to aluminum alloys.
Rumored Buzz on Alcast Company
It permits the production of lightweight elements with exceptional mechanical homes. Zinc boosts the castability of light weight aluminum alloys and helps manage the solidification procedure throughout spreading. It boosts the alloy's stamina and hardness. It is frequently located in applications where intricate forms and fine details are required, such as attractive spreadings and certain automotive parts.
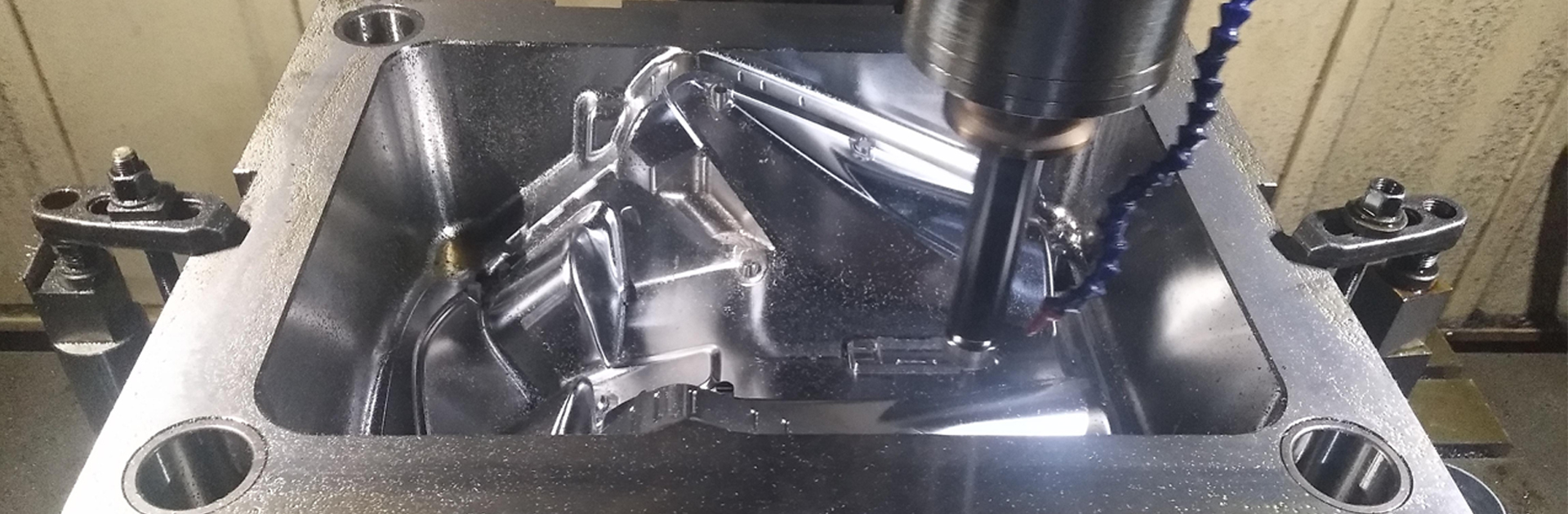
The key thermal conductivity, tensile toughness, yield strength, and elongation vary. Select appropriate basic materials according to the efficiency of the target product created. Amongst the above alloys, A356 has the highest thermal conductivity, and A380 and ADC12 have the most affordable. The tensile limit is the contrary. A360 has the most effective return stamina and the highest possible elongation price.
The Definitive Guide for Alcast Company

In precision spreading, 6063 is fit for applications where intricate geometries and premium surface coatings are extremely important. Examples include telecommunication units, where the alloy's exceptional formability permits sleek and visually pleasing layouts while maintaining structural honesty. In the Illumination Solutions sector, precision-cast 6063 elements create stylish and efficient illumination components that call for detailed forms and excellent thermal performance.
The A360 shows premium prolongation, making it ideal for facility and thin-walled components. In precision casting applications, A360 is fit for sectors such as Customer Electronic Devices, Telecommunication, and Power Tools.
Alcast Company Can Be Fun For Anyone
Its distinct properties make A360 a beneficial choice for accuracy casting in these sectors, enhancing item durability and high quality. Aluminum alloy 380, or A380, is a commonly made use of spreading alloy with several distinct characteristics. It provides excellent castability, making it an excellent option for precision spreading. A380 shows great fluidness when molten, ensuring intricate and detailed molds are accurately replicated.
In accuracy spreading, light weight aluminum 413 radiates in the Consumer Electronic Devices and Power Equipment markets. This alloy's remarkable rust resistance makes it an outstanding choice for outside applications, making certain resilient, durable items in the discussed sectors.
The 8-Second Trick For Alcast Company
Once you have actually chosen that the aluminum pass away casting process appropriates for your project, an important following step is picking the most ideal alloy. The aluminum alloy you select will considerably influence both the casting process and the homes of the end product. Due to this, you have to make your decision very carefully and take an educated strategy.
Figuring out the most appropriate aluminum alloy for your application will imply weighing a vast variety of attributes. The very first category addresses alloy characteristics that influence the production process.
The Only Guide for Alcast Company
The alloy you pick for die spreading directly affects a number of aspects of the spreading process, like just how easy the alloy is to collaborate with and if it is susceptible to casting defects. Warm cracking, additionally understood as solidification cracking, is a common die spreading problem for aluminum alloys that can result in interior or surface-level rips or fractures.
Specific aluminum alloys are much more prone to warm cracking than others, and your choice needs to consider this. It can harm both the actors and the die, so here are the findings you need to look for alloys with high anti-soldering buildings.
Rust resistance, which is already a notable quality of light weight aluminum, can differ substantially from alloy to alloy and is an essential particular to take into consideration relying on the ecological problems your item will be subjected to (Aluminum Castings). Put on resistance is an additional home typically looked for in light weight aluminum items and can separate some alloys
Report this page